Strategic partner for furniture and packaging industries
ORIMAK Cardboard Packaging
Smart, Flexible, and Automated!
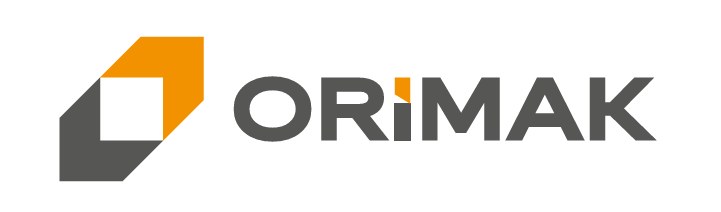
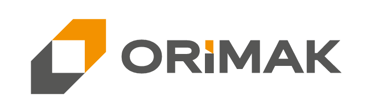
Additional benefits of Q-BOX
Increases efficiency
Reduces labor costs
Lowers the risk of product damage
Minimizes empty space inside the box
Uses less corrugated cardboard
Helps optimize warehouse space
Reduces transportation costs
Enhances customer satisfaction
Promotes environmental sustainability
Q-BOX – automated cardboard box forming
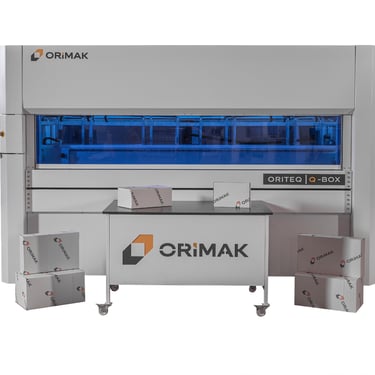
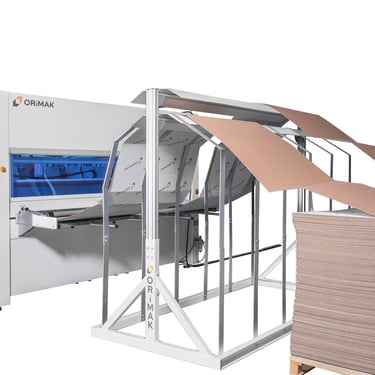
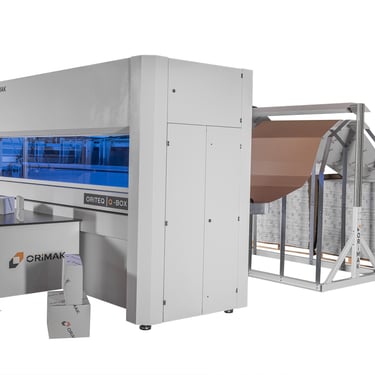
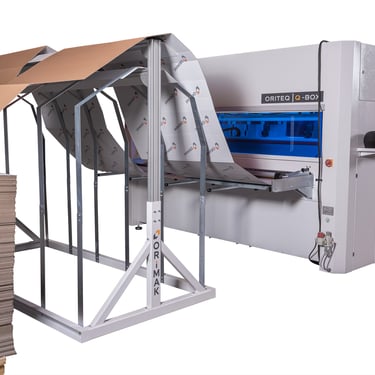
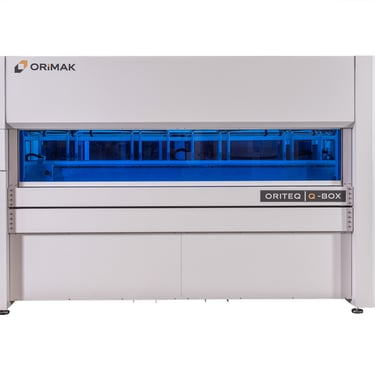
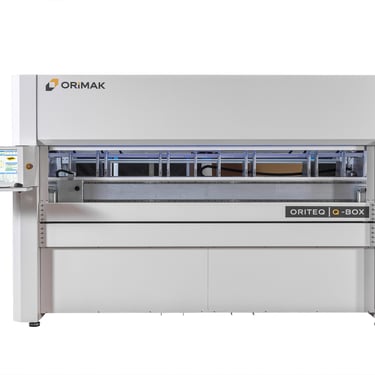
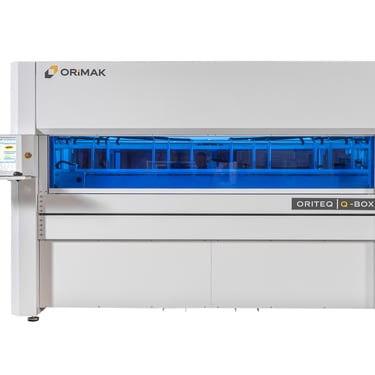
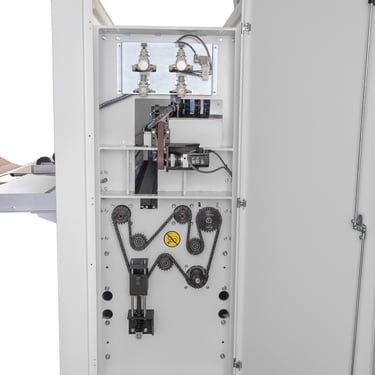
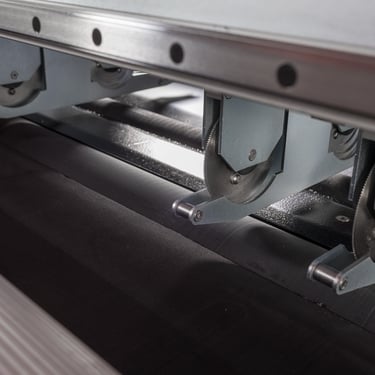
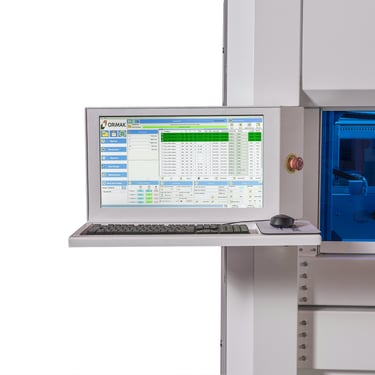
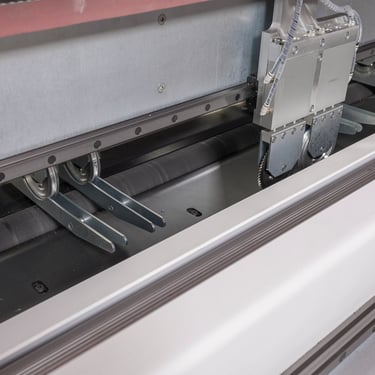
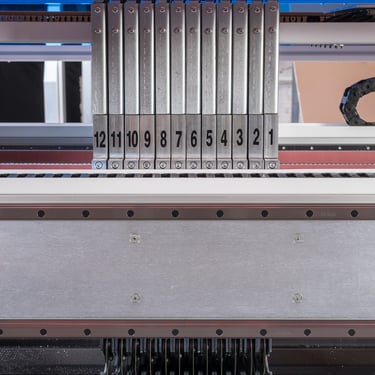

Q-BOX enables automatic cutting of unlimited-length cardboard sheets and forming of crease lines.
Box production with Q-BOX is incredibly simple!
All you need to do is select a pre-programmed box type (FEFCO) and enter the internal dimensions via the touchscreen interface. Thanks to servo-controlled adjustment, all settings are applied automatically in less than a minute. No manual adjustments are required.
Windows operating system, easily compatible with ERP systems
Detailed daily, weekly, or monthly reports available
Cutting direction can be changed to minimize waste and maximize profit
Equipped with 8 vertical cutting knives as standard, expandable to 16 if needed
Punch system for handle cutouts
Automatic measuring system
Wireless barcode scanner
Label printer
Lower costs
There is no need to order a minimum quantity of cardboard boxes. You can produce custom-sized boxes using the cardboard stock already available in your warehouse. Q-BOX automatically creates personalized boxes only when needed. Raw materials are used efficiently, resulting in significant savings on packaging and filler materials.
Time and money savings
Employees no longer waste time searching for the right box sizes for packaging products.
Better protection during transport
You can produce boxes that perfectly match the dimensions of each product, ensuring maximum protection during transportation.
Technical specifications
Cardboard width: min. 200 mm / max. 2600 mm
Cardboard thickness: 2 mm / 7 mm
Boxes per minute: 5–14
Predefined FEFCO box types: 80 different types
Number of vertical knives: 8 (standard) / 9–16 (optional)
Minimum distance between vertical knives: 22 mm
Minimum box height: 22 mm
Cardboard feeding units: 1 (standard) / 4 (optional)
Cardboard feed type: endless length form / sheets
Feeding speed (horizontal): 60 m/min
Feeding speed (vertical): 40 m/min
Power consumption: 2.5 kW
Air pressure: min. 7 bar
Electrical connection: 380–400 V / 50 Hz / 3P–1N–1G
Operating temperature: 10 °C (50 °F) – 40 °C
Software: ORIMAK
Operating system: Windows
Weight: 2240 kg
Qs-BOX automatically cuts cardboard sheets of unlimited length and forms crease lines.
All you need to do is select a pre-programmed box type (FEFCO and/or custom) and enter the internal dimensions via the touchscreen interface. Thanks to servo-controlled adjustments, all settings are automatically configured in under a minute. No manual calibration is required.
Detailed daily, weekly, or monthly reports are available.
If needed, the cutting direction can be changed to reduce waste and maximize profit.
Benefits of ORITEQ Qs-BOX
With Qs-BOX, you can create customized boxes tailored to your product needs. The Windows OS environment allows seamless integration with any ERP or OP system. Qs-BOX eliminates the need for oversized boxes and excess cardboard storage, helping protect your products from damage while reducing waste. Additionally, Qs-BOX enables the production of 100% sustainable and eco-friendly packaging.
Qs-BOX – automated cardboard box forming
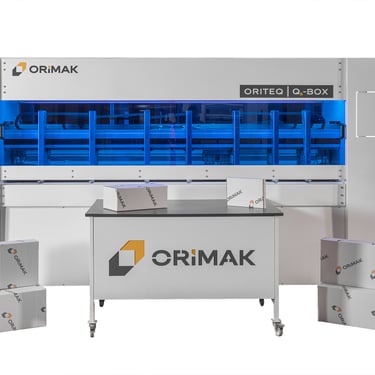
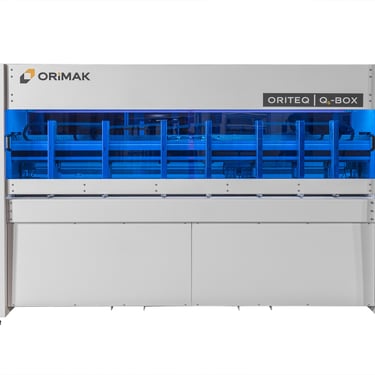
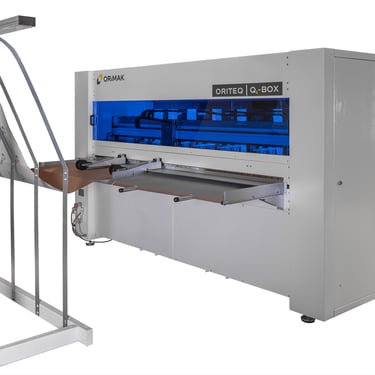
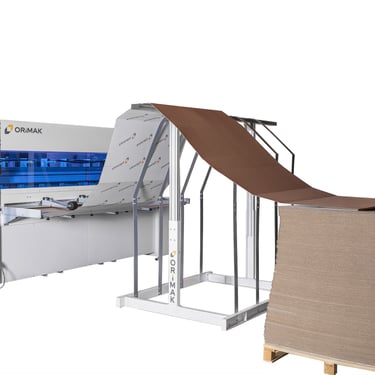
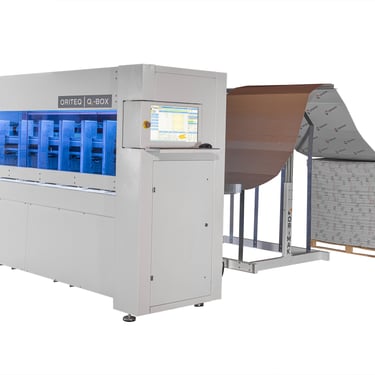
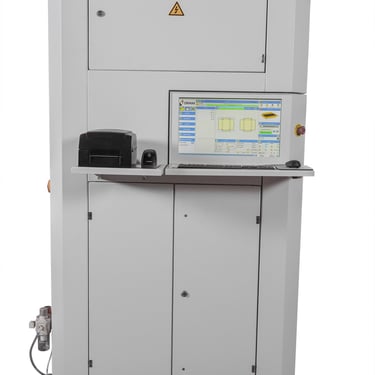
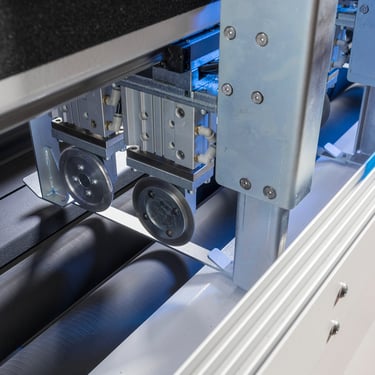
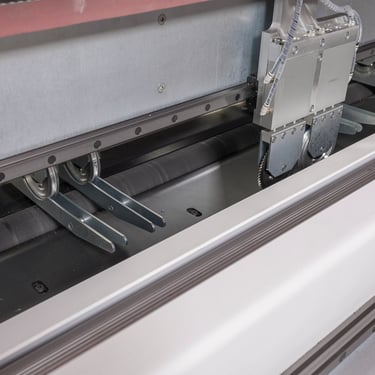
Lower costs
There is no need to specify a minimum order quantity for boxes. You can produce custom-sized boxes based on the amount of cardboard available in your warehouse. Qs-BOX automatically creates personalized boxes only when needed. Raw materials are used efficiently, significantly reducing packaging and filler costs.
Time and cost savings
Employees no longer waste time searching for the right box size for each product.
Better protection during transport
You can produce boxes that perfectly match the dimensions of each product, providing better protection during transportation.
Technical specifications
Cardboard width: min. 300 mm / max. 2400 mm
Cardboard thickness: 2 mm / 7 mm
Boxes per minute: 5–10
Predefined FEFCO box types: 55 different types
Number of vertical knives: 7 (standard)
Minimum distance between knives: 25–75 mm
Minimum box height: 25 mm
Cardboard feeding units: 1 (standard)
Cardboard feed type: endless form / sheets
Feeding speed (horizontal): 60 m/min
Feeding speed (vertical): 40 m/min
Power consumption: 1.5 kW
Air pressure: min. 7 bar
Electrical connection: 380–400 V / 50 Hz / 3P–1N–1G
Operating temperature: 10 °C (50 °F) – 40 °C
Software: ORIMAK
Operating system: Windows
Weight: 1500 kg

Technical specifications
Sheet width: 2100 mm
Cutting height of cardboard: min. 10 mm / max. 100 mm
Cardboard feeding: manual
Power supply: 3 kW
Air pressure: min. 7 bar
Electrical connection: 380–400 V / 50 Hz / 3P–1N–1G
Operating temperature: 10 °C (50 °F) – 40 °C
Software: ORIMAK
Operating system: Windows
Weight: 1500 kg
H-CUT honeycomb board cutting solution
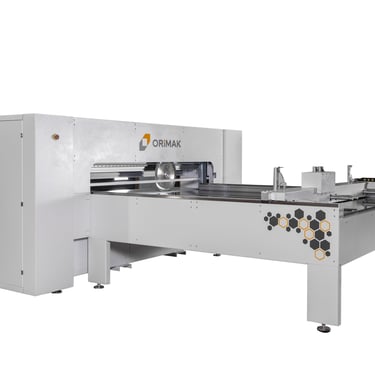

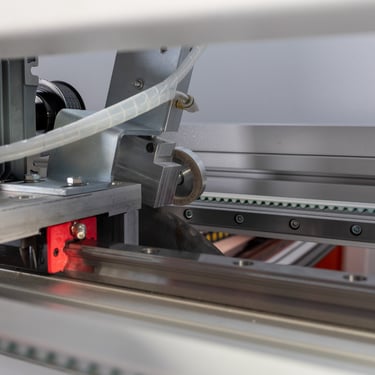
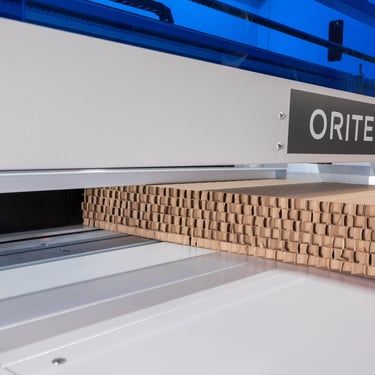
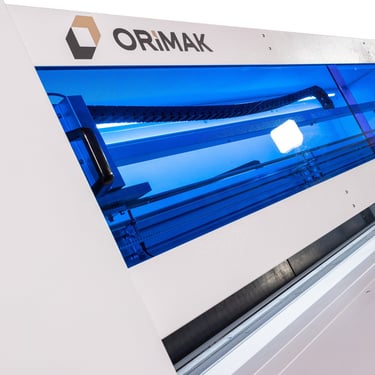
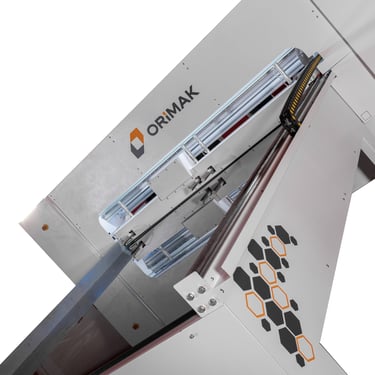
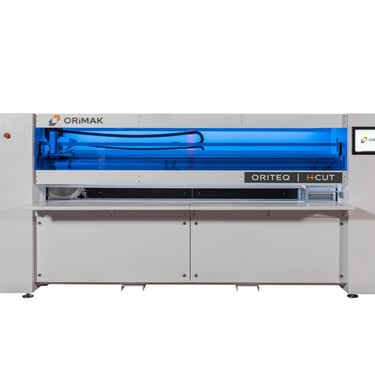
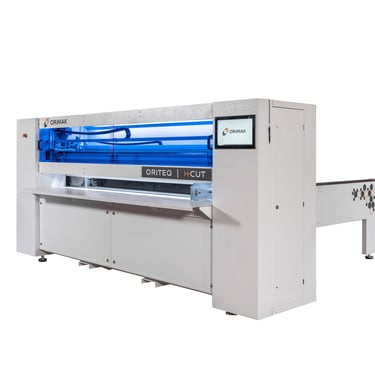
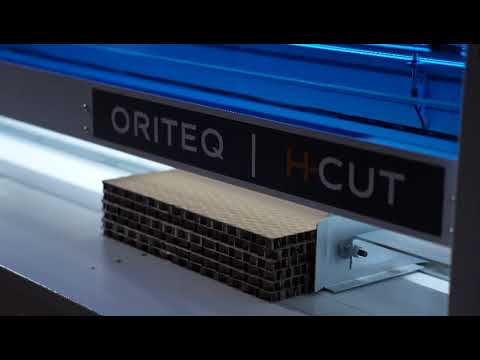
Using the H-CUT honeycomb cutting machine, you can cut honeycomb cardboard to your desired dimensions, tailored to your specific needs.
Save time and reduce costs. Improve protection during transportation.
With the H-CUT honeycomb cutting system, you can cut honeycomb board to custom sizes that match your requirements.
Advantages:
Saves time and reduces costs
Ensures better protection during transportation
Easily integrates with any MES or ERP system
Industry 4.0 ready
Technical specifications
Maximum output (per minute): 4–8 units
Minimum box length: 300 mm
Maximum box length: 3000 mm
Minimum box height: 30 mm
Maximum box height: 300 mm
Minimum box width: 250 mm
Maximum box width: 1250 mm
Installed power: 25 kW
Machine weight: 3500 kg
Maximum package weight: 60 kg
ORİTEQ BC410 Pro – automatic box sealing machine

Using the ORİTEQ BC410 Pro box closing machine, side flaps of product-filled boxes (FEFCO 410) are sealed using hot melt technology, ensuring high quality and cost-efficiency.
An automated box measurement system eliminates the need for manual input of varying package sizes. The closing mechanisms quickly and fully automatically seal the box flaps.